Most pump equipment requires particular types and amounts of lubrication. It should be a top priority on any maintenance plan.
Lubricate the motor and bearings according to the manufacturer’s guidelines. Be careful not to over-lubricate; more bearing damage occurs from over-greasing than under-greasing.
Clean the motor vents to remove any dust build-up. Remember to shut down and de-energize the machine before inspecting or performing maintenance.
Check the Fluid Level
Regarding hydraulic systems, pumps and motors New York, NY plays a vital role in their operation. They help lift heavy loads, press parts, and complete tasks more efficiently. However, these units are susceptible to breakdowns and expensive repairs like machines. Fortunately, an efficient maintenance program will keep them running well for years.
One of the most common reasons a pump malfunctions is low fluid levels. When the system isn’t lubricated properly, it can cause misalignment and other issues that lead to tripping or premature bearing failure.
Locate the bay to check the hydraulic fluid level. The dipstick may have indicators for full and low, or the reservoir itself might have those markings molded into it.
Pull out the dipstick, wipe it clean, then carefully insert it back and look for the indicators.
It is time to replace the hydraulic fluid and use the type specified by the manufacturer to avoid damage.
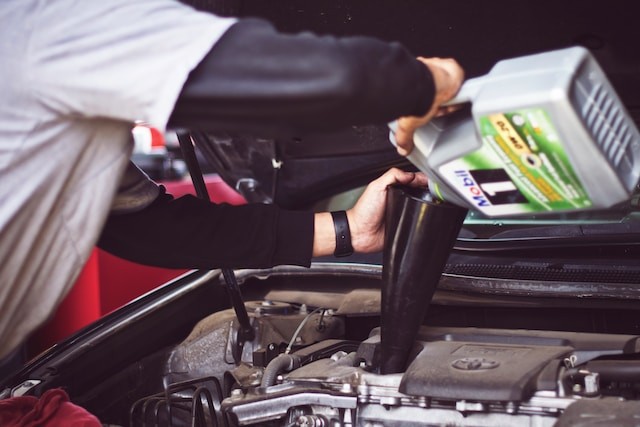
Rotate the Input Shaft
Pumps are integral to many operations, but they can take time to keep up with. That’s why you should implement a regular maintenance schedule to help reduce costly repairs.
Preventive maintenance includes planned inspections and services based on the number of hours run. A visual inspection is a simple way to spot problems like leaks and wear. It also involves lubrication, gasket care, and cleaning procedures.
Rotating the input shaft helps to check for bearing and shaft wear. It can be done with a hand crank or mechanically assisted with the removal of set screws and machined strainer studs (where present).
The final step of preventive maintenance is to apply a light layer of rust inhibitor to all exposed metal surfaces before storing. Rust can cause severe damage if not treated quickly. It will help the pumps to perform optimally when in use. In addition, it will prevent the need for expensive corrective maintenance.
Lubricate the Bearings
It is essential to check the condition of the bearings. These are the critical components of the motor that connect the shaft to the housing. It can shorten the motor’s life when not in good condition.
Manuals usually recommend greasing the bearings every 4000 operating hours with 0.8 ounces of fresh grease. It is a reasonable guideline, but implementing it is a challenge.
One problem is that knowing when to re-grease can take a lot of work. A good solution is to use ultrasound monitoring during the re-greasing process. When the acoustic feedback indicates that the friction is at or below minimum levels, stop greasing!
Another essential technique is to remove the bottom drain plug during re-greasing. It will allow the mechanical action of the motor to help expel old grease through the relief passage and allow pressure equalization in the bearing housing as new grease is pumped in.
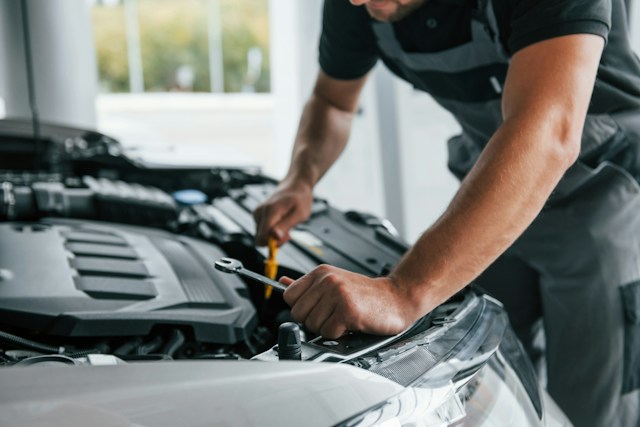
Inspect the Motor
The pump’s functionality heavily depends on the motor, a crucial component. It provides the power to drive the impeller, which causes water flow and boosts kinetic energy. Keeping your engine in good working condition is essential to prevent costly repairs and replacements.
Regularly checking the motor for leaks, unusual sounds or vibrations, and performance loss is essential. Using a multimeter to test the windings for resistance can also help identify issues. Typically, values in the single digits indicate an excellent reading. Values significantly higher than that can mean the winding has opened or shorted.
Lastly, you should check the direction of rotation of the shaft. Usually, this is indicated on the motor bearing frame. Electricians often use “bumping” the motor to check for proper shaft rotation.